Product Description
Stainless steel casting, also called stainless steel investment casting, refers to the formation of ceramics around a wax pattern to form a shell for casting stainless steel. Once wax patterns are created, they are melted into the gate system, immersed in slurry and sand to form a layered shell, and then replaced by molten stainless steel.
Stainless steel casting involves creating an original wax model, building the image with plaster and successive layers until a strong shell surrounds the model. After melting the wax, pour the molten stainless steel into the mold to create a perfect replica of the original wax pattern. Stainless steel casting provides economical undercutting, high resolution, sophisticated detail and smooth surface finish compared to machining separations. In most cases, stainless steel casting is the only way the part can be made economically. How are Stainless Steel Castings Made?
Advantages of Stainless Steel Casting
- Sizes: 0.1 in to 24 in
- Weights: a few grams to more than 50 pounds
- Surface: very smooth finish
- Tight tolerances
- Reliable process controls and repeatability
- Design and casting versatility
- Efficient production
- Affordable tooling
- Material variety
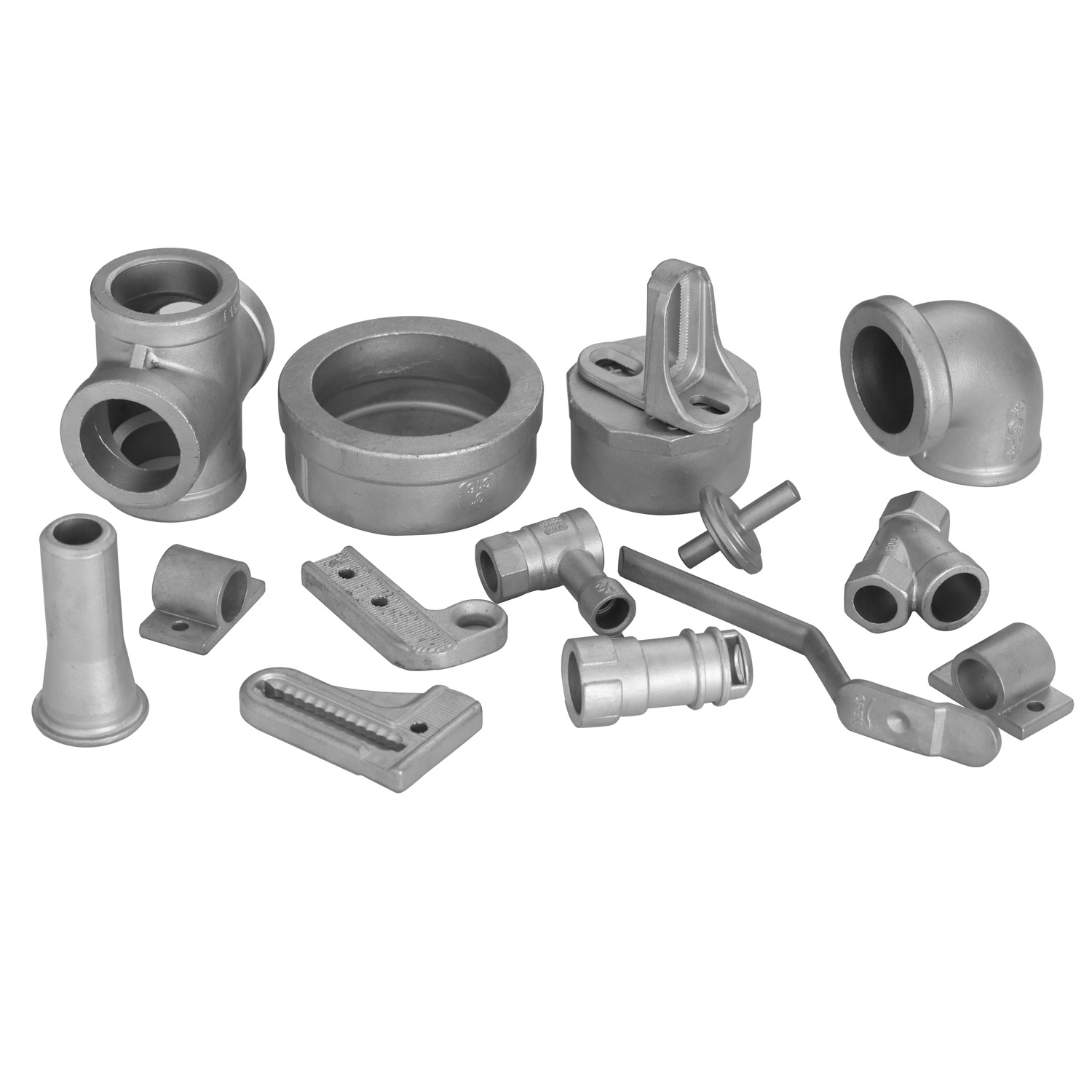
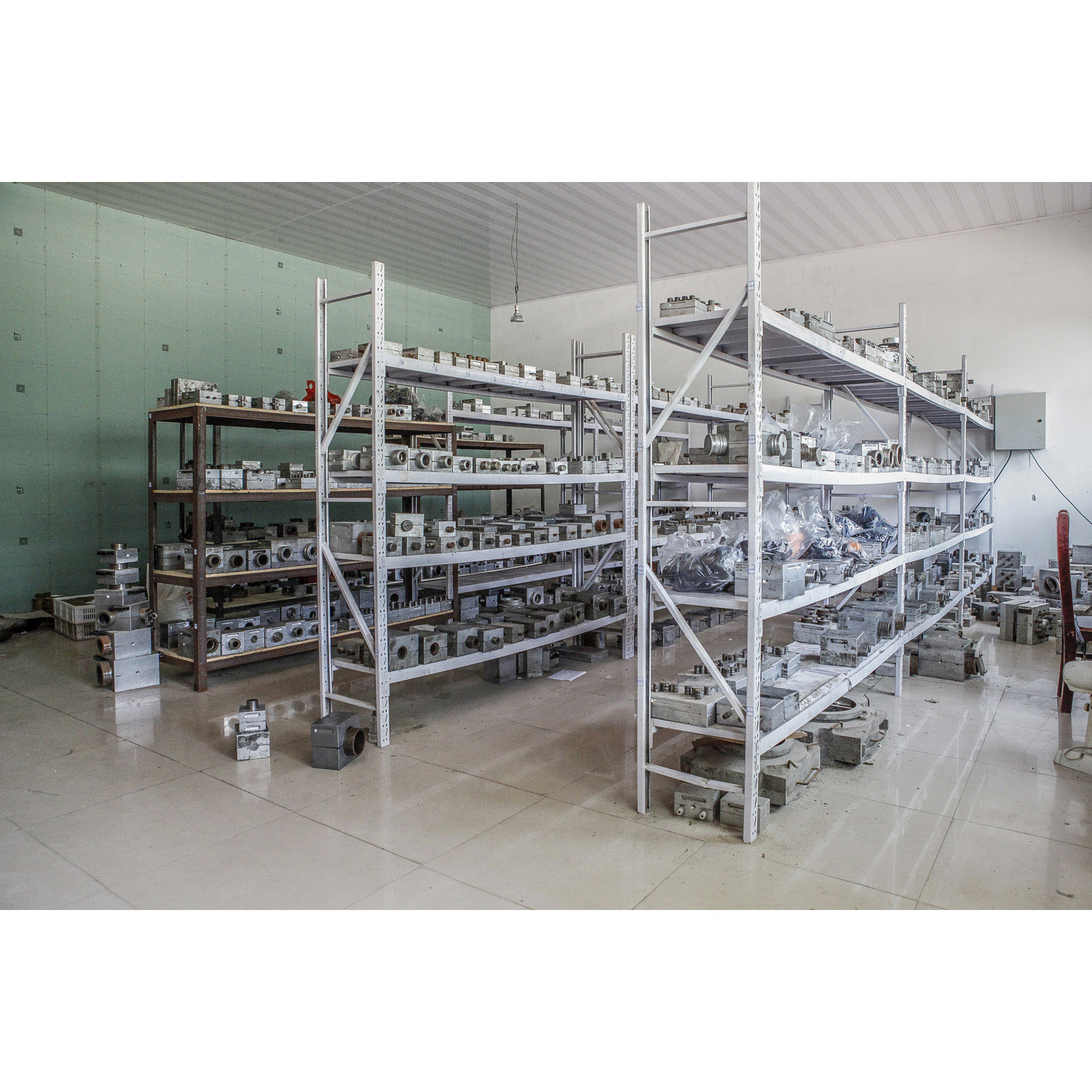
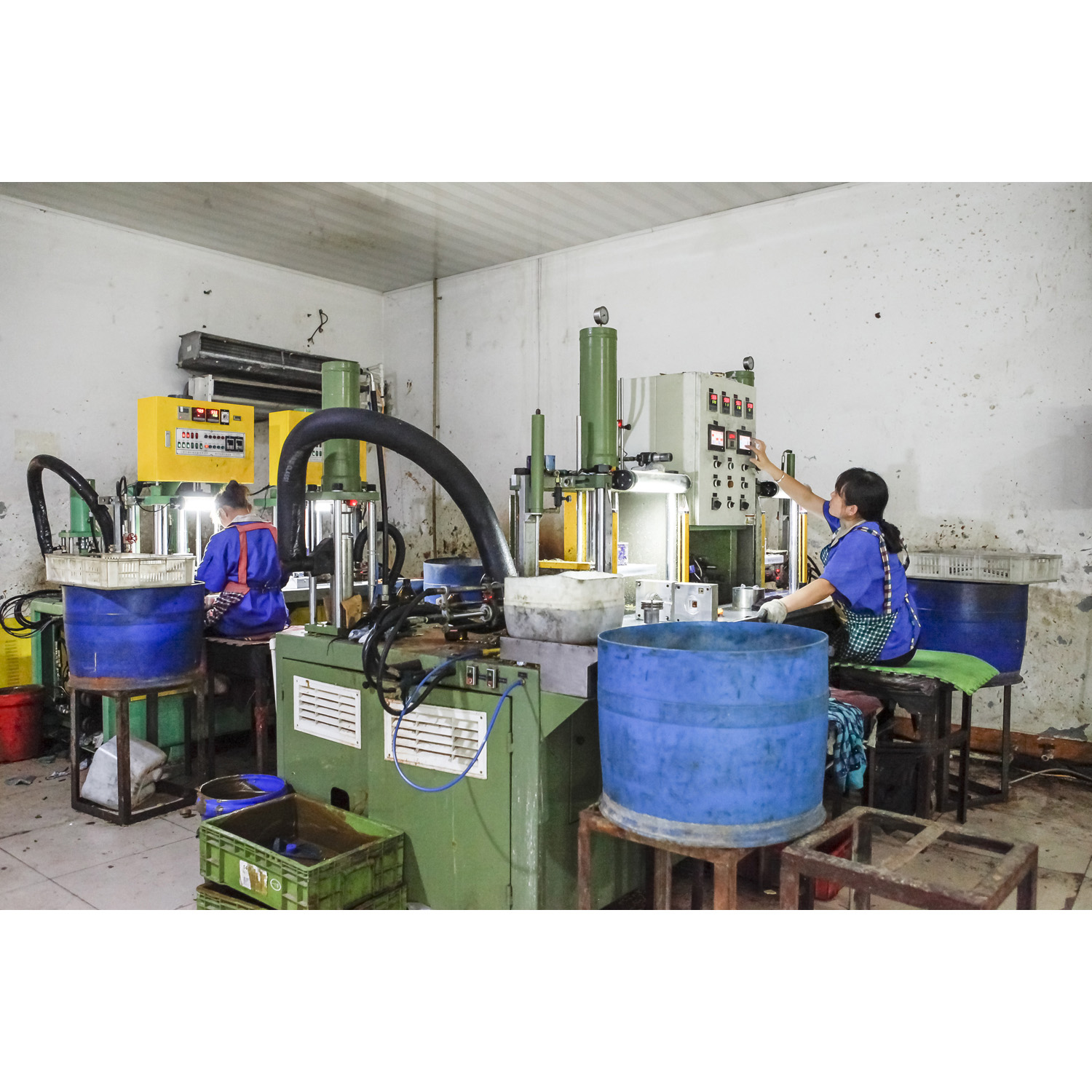
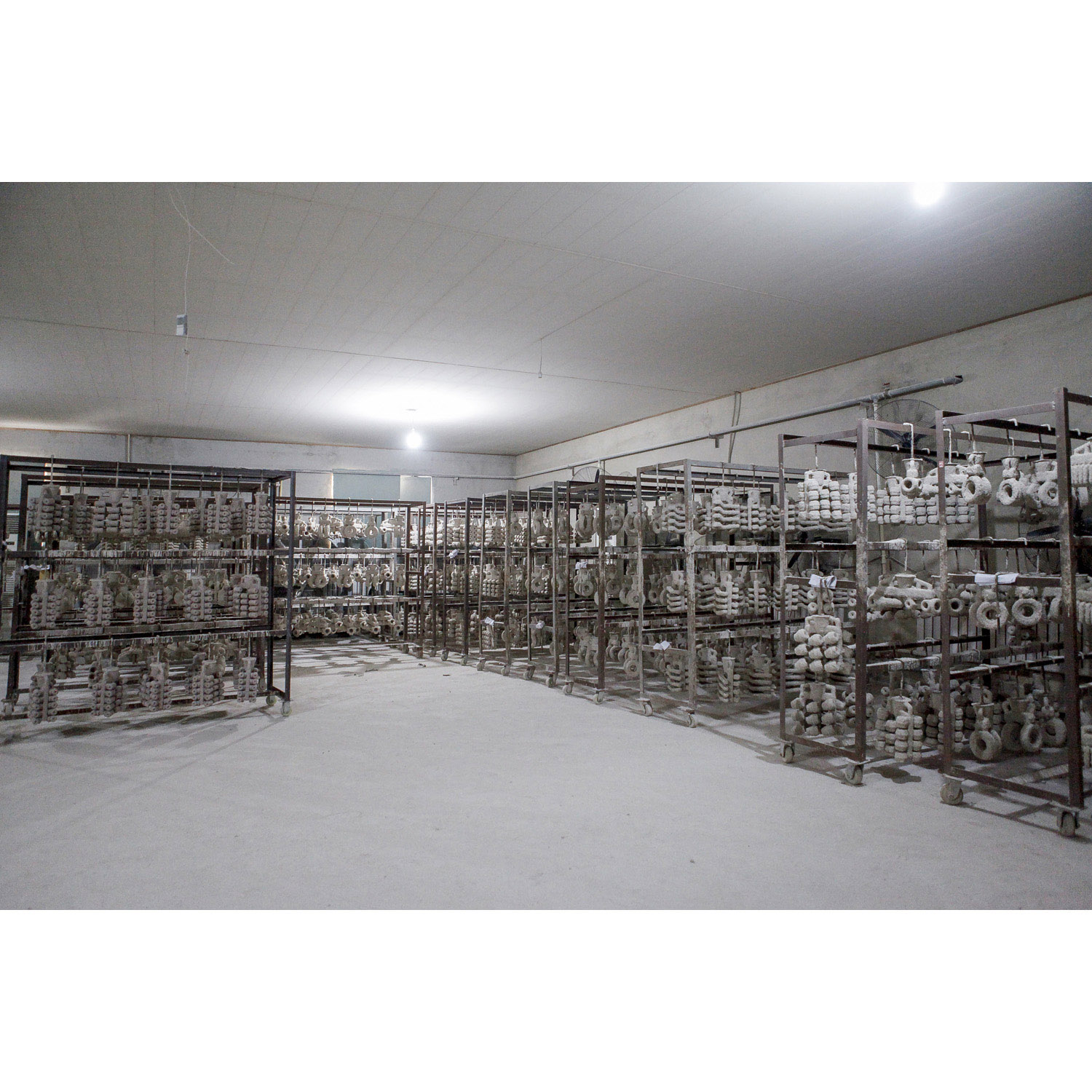
