The investment casting process begins with a pattern. Traditionally, the pattern was injection mould in foundry wax. Gates and vents are attached to the pattern, which is then attached to the pure. After all patterns are mounted to the sprue producing what is called casting tree. At these points casting is ready for shelling. The casting tree is repeatedly dipped in ceramic slurry to create a hard shell that is called investment. The patterns are then melted out (also called burnout) of the investment, leaving a cavity in the shape of the part to be cast.
A metal alloy is melted, often in induction furnace, and poured into the preheated investment. After cooling, the shell is broken away, the metal parts are cut from the tree and gates and vents are ground off.
Our factory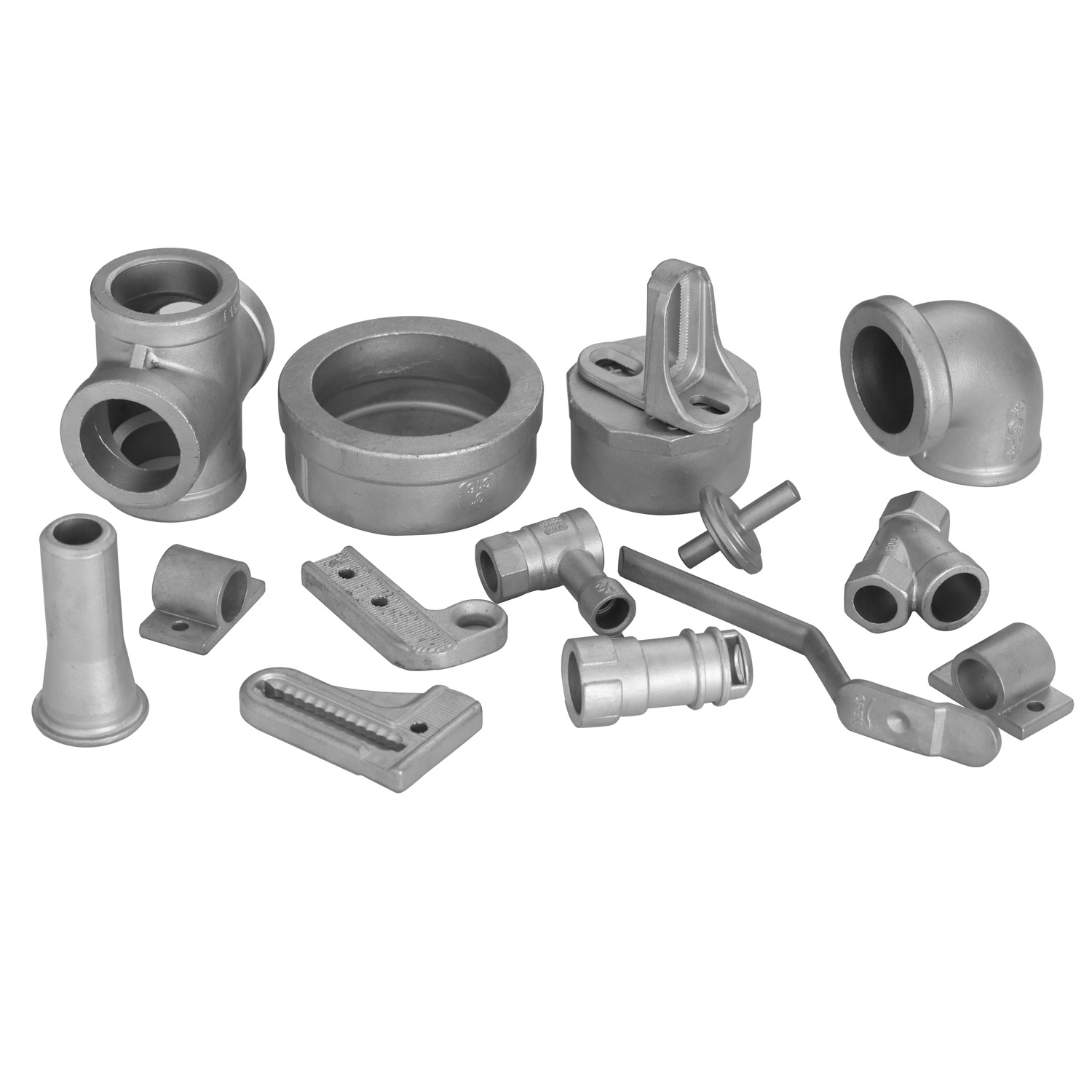
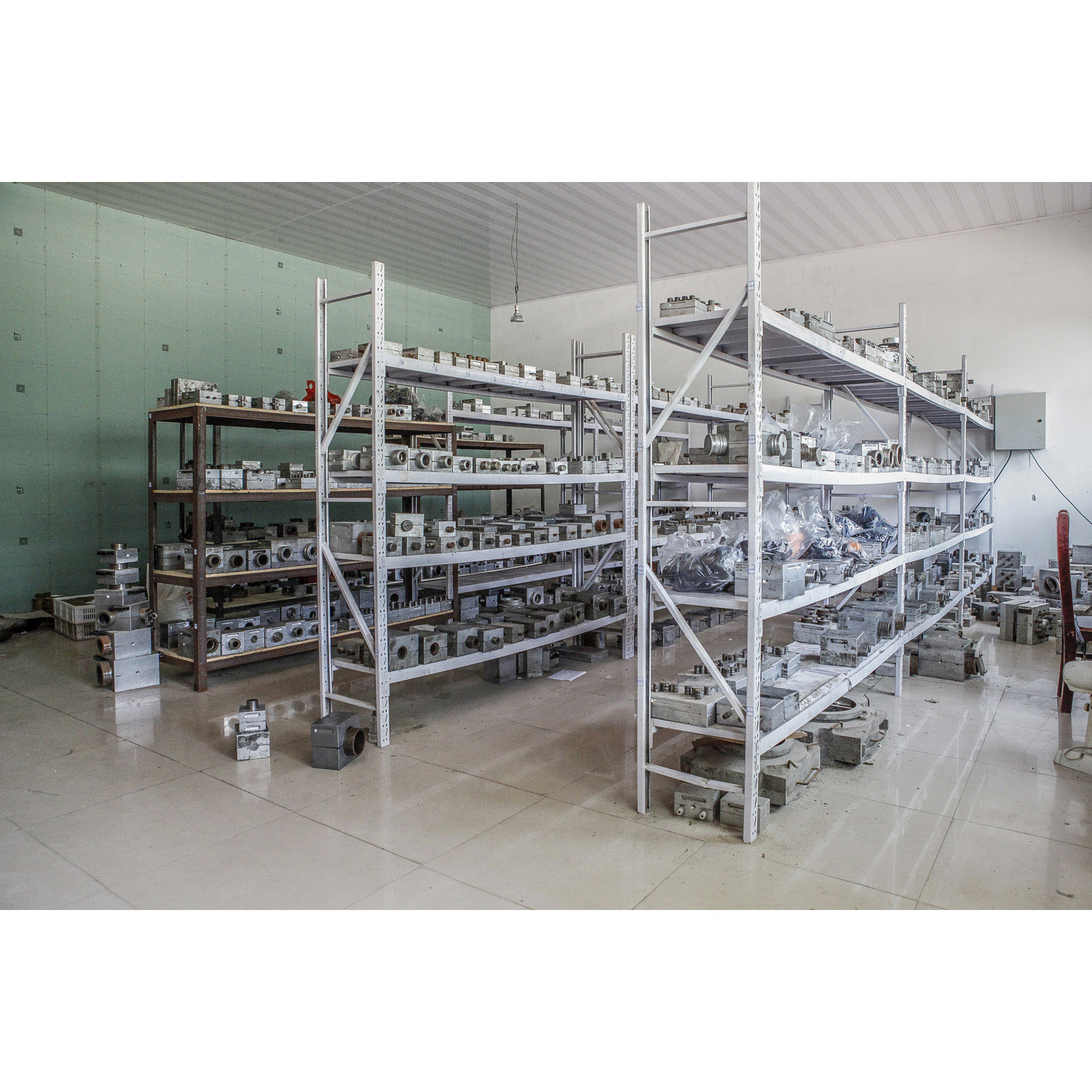
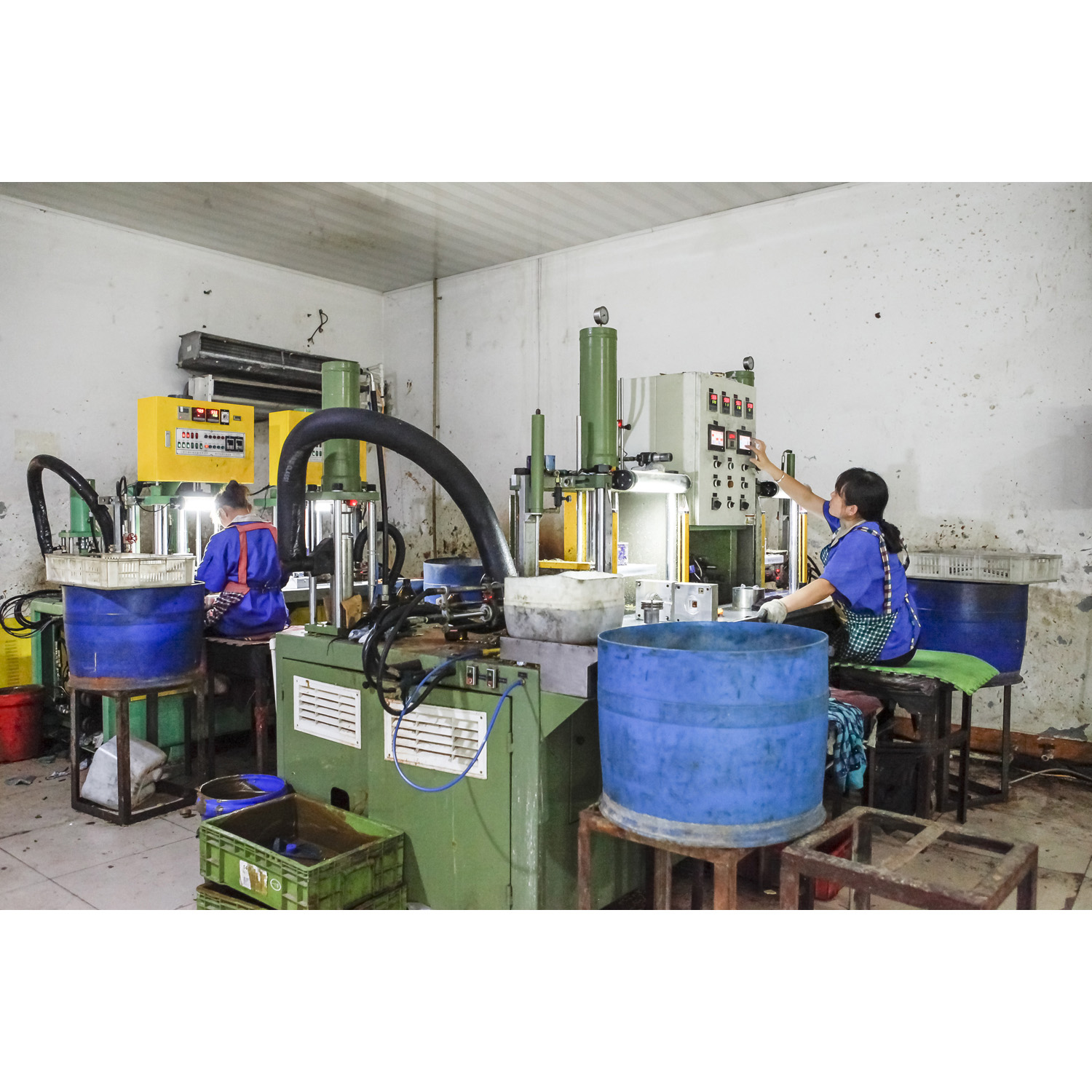
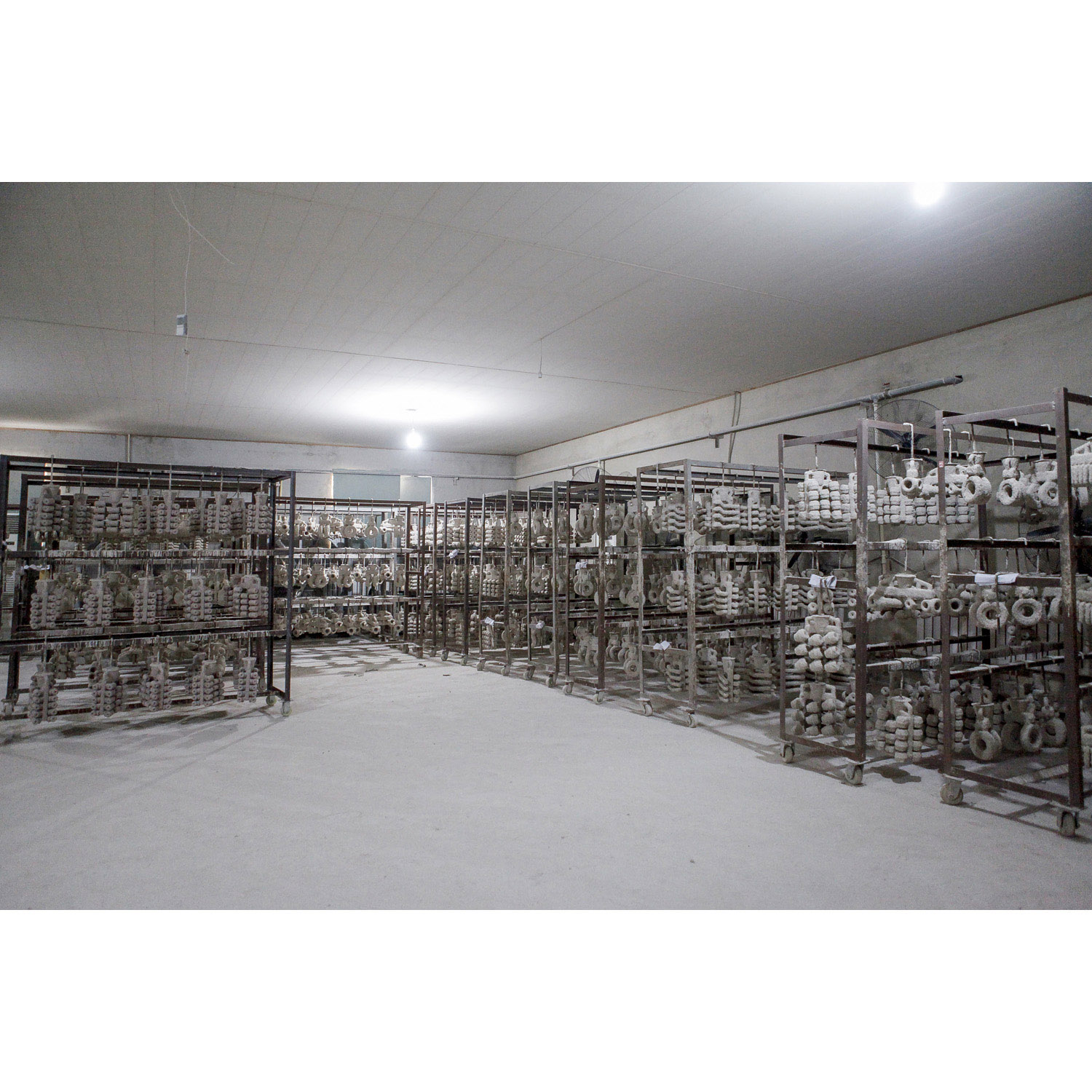
